Understanding Hot Air Solder Leveling (HASL) in PCB Manufacturing
Hot Air Solder Leveling (HASL) has long been a preferred surface finish in PCB manufacturing, valued for its cost-effectiveness and excellent solderability. This process involves several key steps: cleaning, fluxing, and applying molten solder to achieve optimal wetting, followed by removing excess solder using hot air knives.
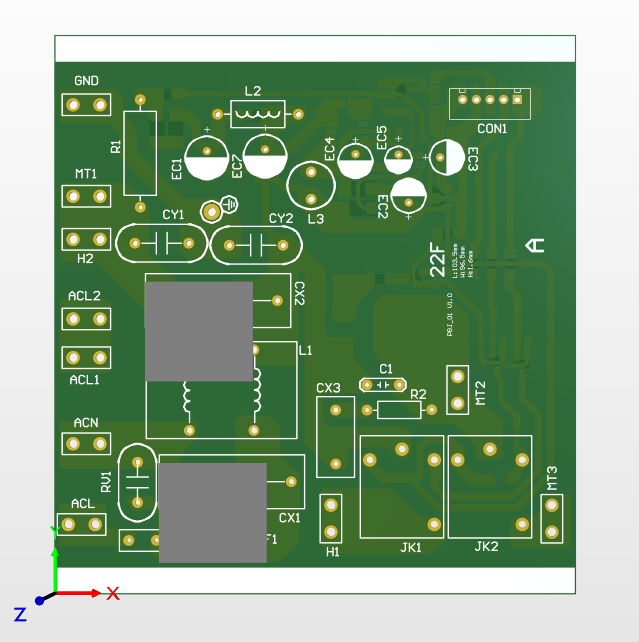
Application and Process
HASL can be applied either vertically or horizontally. Vertical immersion ensures thorough solder coverage, while horizontal application, using nozzles or rollers, offers superior uniformity. This makes HASL ideal for through-hole and larger SMT components, though it may not suit fine-pitch components due to its thickness.
Advantages and Disadvantages
The advantages of HASL include its economic viability, good shelf life, and reworkability. However, it faces challenges with environmental regulations like RoHS compliance, and its suitability for fine-pitch components and plated through-holes can be limited. Careful consideration of these factors is crucial in modern PCB manufacturing.
Transition to Lead-Free HASL: Driven by stricter environmental standards, many companies are transitioning to lead-free HASL. This alternative uses eco-friendly alloys, resulting in smoother finishes and eliminating issues with coplanarity on pads like BGA and CSP. Lead-free HASL also maintains solderability through various reflow profiles, meeting evolving industry demands.
Key Considerations: When choosing between HASL and lead-free alternatives, manufacturers must balance cost-effectiveness, environmental impact, and technical requirements. Understanding these trade-offs is essential for optimizing PCB design and manufacturing processes.
Explore how HASL and lead-free HASL contribute to PCB design and compliance with environmental standards, ensuring robust performance and sustainability in electronics manufacturing.
Pingback: Why Choose CEN PCBA Over PCB Manufacturing Brokers: The Advantages of Direct Manufacturing - Contract Manufacturing
Comments are closed.