The evolution of drones has seen them emerge as essential tools across various industries, from defense and agriculture to construction and logistics. One of the key innovations driving this advancement is the integration of advanced sensor technologies, which enable features like autonomous navigation, obstacle avoidance, and real-time data collection. As drones become more sophisticated, ensuring that their sensors are seamlessly integrated into the printed circuit board assemblies (PCBAs) has become a significant challenge for designers and manufacturers.
In this article, we will delve into the specific challenges associated with sensor integration for drone PCBAs, explore best practices to overcome these hurdles, and provide valuable insights into creating robust and efficient drone PCBAs that support critical sensor technologies. By addressing these challenges, manufacturers can position themselves as key players in the evolving drone market.
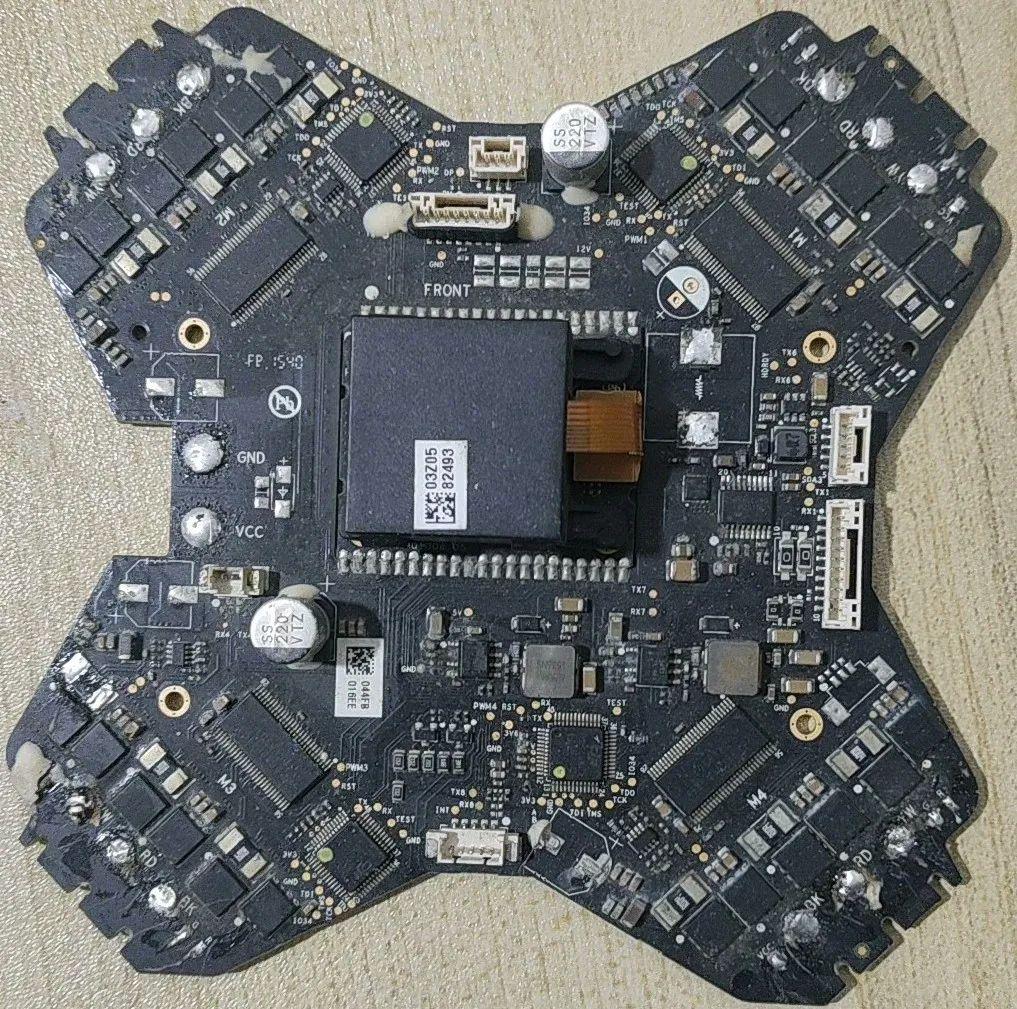
The Role of Sensors in Drones
Drones rely on various sensor technologies to perform tasks with precision, reliability, and efficiency. These sensors are crucial for navigation, environmental monitoring, and data collection, which are essential for industries such as defense, agriculture, and logistics. Some of the most commonly used sensor technologies in drones include:
- RGB Cameras: Used for capturing high-resolution images in visible light for applications such as land use mapping and environmental monitoring. However, they are sensitive to lighting changes and glare, limiting their usefulness in low-light conditions.
- Multispectral and Hyperspectral Cameras: These cameras capture images in spectral bands beyond visible light, providing insights for applications like crop health monitoring. While multispectral cameras offer higher resolution and are more affordable, hyperspectral cameras provide more detailed material analysis but are more expensive and complex.
- Thermal Cameras: Detect infrared radiation to measure heat and identify anomalies, useful for search and rescue, power line inspection, and building diagnostics. These cameras may suffer from vibrations and limited field of view.
- LiDAR: Uses laser beams to measure distances and create 3D models, useful for terrain mapping and flood modeling, but expensive and requiring specialized training.
- Radar Sensors: These measure the distance and speed of objects using radio waves, enabling effective long-range detection and operation in various weather conditions.
For a drone to perform optimally, it requires precise data processing and integration of these sensors. However, incorporating such diverse and powerful technologies into the compact design of a drone presents multiple design challenges.
PCBA Challenges in Sensor Integration
As drones become more advanced, their PCBA designs must evolve to handle the integration of high-speed, high-performance sensors within a constrained physical space. The following are some of the key challenges that designers face:
- Signal Integrity: Compact designs make it difficult to separate analog, digital, and mixed signals. Close component placement leads to signal interference (crosstalk) and inefficient routing, which can degrade performance. Signal integrity issues can be exacerbated by small trace spacing and high-frequency sensor signals.
- Thermal Management: The compact size of drones means that heat dissipation becomes a critical concern, especially with high-powered sensors. Unmanaged heat can lead to performance degradation and component failure. Designers must carefully select components that minimize heat output and implement effective cooling strategies.
- Power Management: The small batteries on drones make efficient power consumption essential. Sensors and communication systems often draw significant power, and balancing this with the drone’s limited battery capacity can be difficult. Power-efficient components and low-power communication protocols are essential for optimizing flight time.
- Miniaturization and Component Placement: Miniaturization offers the advantage of creating smaller, lighter drones, but it also requires careful component placement to ensure adequate spacing between components. Dense layouts can result in poor performance and increased difficulty in inspecting and manufacturing the PCBA.
- Data Speed and Processing: As drones employ more sophisticated sensors, the amount of data generated increases exponentially. The PCBA design must support high-speed data transmission and processing, without introducing noise or electromagnetic interference (EMI).
- Analog-to-Digital Conversion: Drones often utilize analog sensors that need to be converted into digital signals for processing by the flight controller. Designing the interface between analog sensors and digital systems can be challenging, particularly when an anti-aliasing filter is omitted, leading to data inaccuracies.
Design Tips and Best Practices for Overcoming PCBA Challenges
To overcome these challenges and ensure the success of sensor integration in drone PCBAs, designers can follow several best practices:
1. Prioritize Signal Integrity:
- Manually route critical parts of the circuit to avoid errors associated with autorouters, especially for high-speed signals.
- Separate analog, digital, and mixed signal components to minimize noise interference and ensure clean signal paths.
- Implement continuous ground and return planes to minimize noise coupling.
- Use bypass capacitors to reduce power noise and ensure stable sensor performance.
2. Optimize for Thermal Management:
- Use components that generate less heat and place them strategically to reduce heat dissipation near critical areas.
- Implement heat sinks or enclose heat-sensitive sensors in protective materials to manage thermal stress.
- Employ conformal coatings to protect sensors from temperature fluctuations and environmental conditions.
3. Improve Power Efficiency:
- Utilize low-power sensors and communication protocols, such as Bluetooth Low Energy (BLE) or Wi-Fi HaLow, to extend battery life.
- Consider power harvesting methods, such as integrating solar panels or piezoelectric materials, to provide supplementary power during flight.
- Implement power management techniques like Dynamic Power Management (DPM) and power gating to optimize energy use.
4. Ensure Data Integrity:
- Attach anti-aliasing filters to the input of Analog-to-Digital Converters (ADCs) to avoid sampling errors.
- Use signal isolation techniques to prevent cross-talk between high-speed sensor signals and less sensitive circuits.
- Optimize PCB traces for high-speed signal transmission to reduce electromagnetic interference (EMI).
5. Collaborative Approach:
Collaboration between designers, manufacturers, and sensor component suppliers is essential. Open communication ensures that sensor technologies are integrated seamlessly and that the PCBA design meets the exact needs of the drone.
Drones have proven to be powerful tools across a variety of industries, offering advantages in efficiency, safety, and data collection. However, integrating advanced sensors into the PCBA design of a drone requires overcoming several technical challenges, including signal integrity, thermal management, power efficiency, and data processing. By following best practices and collaborating closely with other stakeholders, designers can overcome these hurdles and create robust drone PCBAs that support the cutting-edge sensor technologies that are revolutionizing industries today.
At CEN PCBA, we specialize in overcoming these challenges, offering comprehensive PCBA design, manufacturing, and assembly services tailored to the needs of drone manufacturers. Whether you are integrating sensors for military, agricultural, or commercial drones, our team is equipped with the expertise and capabilities to bring your innovative designs to life.